How to Optimize Operational Monitoring for IoT Integration and Predictive Maintenance in Manufacturing
- satyashukla
- Mar 5
- 4 min read
In today’s competitive manufacturing landscape, operational monitoring has emerged as a cornerstone of efficiency and productivity. The integration of Internet of Things (IoT) devices into industrial environments has transformed how businesses track performance metrics and respond to anomalies. This blog post will explore strategies for optimizing operational monitoring, focusing on real-time data collection through IoT, data visualization, process stability, predictive maintenance, and more, ensuring your manufacturing processes are both efficient and reliable.
IoT Integration
By integrating IoT devices into manufacturing processes, companies can collect performance data from machinery and production lines in real-time. This data provides invaluable insights that can be leveraged to improve operations and minimize downtime.
Real-time data collection enables manufacturers to monitor equipment conditions and production flow continuously. IoT sensors track key performance indicators (KPIs) such as equipment temperature, vibration, and operational speed. These metrics offer a comprehensive view of machinery health and performance, allowing teams to make informed decisions based on current conditions.
The effective use of IoT not only enhances visibility but also strengthens the decision-making process. When performance and operational data are readily available, manufacturers can react proactively rather than reactively. This shift can lead to greater levels of efficiency and reduced costs over time.
Data Visualization
Once performance data is collected, the next step is to visualize it effectively. Data visualization tools enable manufacturers to track and display performance metrics over time, helping identify trends and anomalies that could signal potential issues.
Graphs, dashboards, and infographics can present data in a way that is easy to digest and understand. By using these visualization techniques, manufacturers can quickly detect patterns that might indicate inefficiencies or equipment failures. This not only aids in real-time monitoring but also supports long-term strategic planning as manufacturers can recognize and predict trends over time.
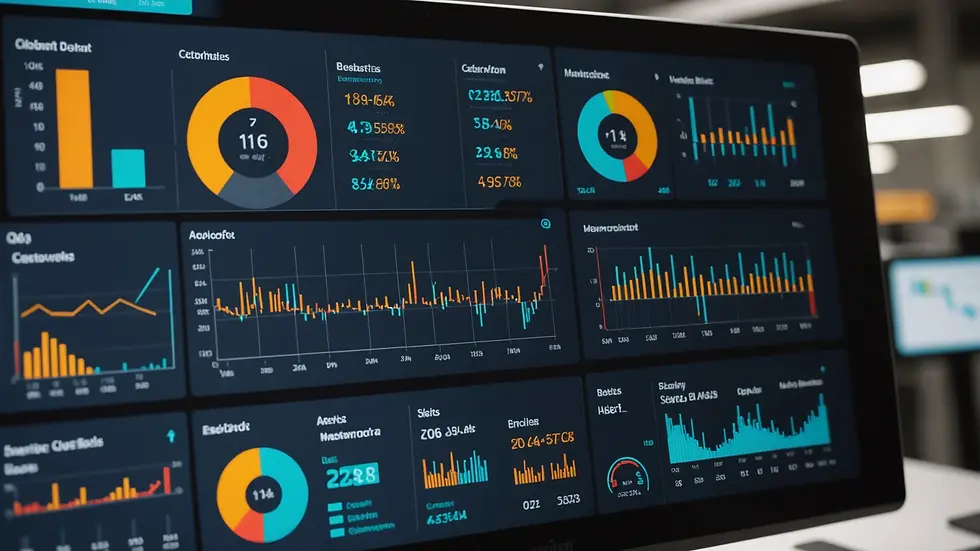
Data visualization not only enhances individual and team understanding but can also foster collaboration across departments. When different areas of a business can visualize the same data, they can align their efforts more effectively, resulting in a more efficient operational approach.
Process Stability
Ensuring process stability is vital for maintaining product quality and operational efficiency. Among the tools available, control charts are a crucial element in monitoring manufacturing processes.
Control Charts
Control charts provide a graphical method for tracking process data over time, determining whether a process is in control or if adjustments are needed. By establishing control limits based on historical performance data, manufacturers can quickly identify variances that may indicate process instability.
Control charts not only capture data but also contribute to process improvement initiatives. By keeping track of performance metrics, manufacturers can ensure that processes remain stable and within control limits, leading to increased product quality and reduced waste.
Statistical Analysis
Alongside control charts, applying statistical analysis techniques allows manufacturers to identify variations in process behavior. Techniques such as hypothesis testing, regression analysis, and capability studies can pinpoint issues and guide corrective actions promptly.
By understanding the root causes of variation, manufacturers can implement changes that enhance process stability. This proactive approach reduces the risk of product defects and significantly decreases costs associated with rework and scrap.
Predictive Maintenance
Moving beyond reactive maintenance modalities, predictive maintenance offers a more strategic approach to equipment upkeep. With a focus on anticipating failures before they occur, predictive maintenance transforms the relationship between maintenance schedules and equipment health.
Historical Data Analysis
One of the foundational elements of predictive maintenance is the analysis of historical data. By examining past performance and failure patterns, manufacturers can predict when maintenance is needed, thereby limiting unexpected downtimes.
Historical data analysis serves as a built-in safety net. Using this data, manufacturers can develop a maintenance schedule that aligns with actual equipment needs rather than relying on arbitrary timelines. This not only saves money on unnecessary maintenance but also ensures that machinery operates at peak performance levels.
Machine Learning
Incorporating machine learning algorithms takes predictive maintenance to the next level. These algorithms analyze both historical and real-time data to recognize complex patterns and forecast equipment failures.
By leveraging machine learning, businesses can create predictive models that provide insights not only into when a machine may fail but also into the factors leading to that failure. This enhanced foresight allows manufacturing teams to take predefined actions, significantly reducing unplanned downtime and maintenance costs.

Conclusion
As the manufacturing landscape continues to evolve, optimizing operational monitoring through IoT integration and predictive maintenance is crucial for maintaining competitiveness. The implementation of real-time data collection, effective data visualization, robust process stability measures, and strategic predictive maintenance can transform the efficiency and effectiveness of any manufacturing operation.
By harnessing the power of IoT and advanced data analysis techniques, manufacturers can improve operational transparency, ensure process stability, and minimize unexpected equipment failures. Ultimately, this commitment to operational excellence prepares organizations to thrive in an increasingly connected and data-driven future.
Embracing these strategies will not only enhance productivity but will also position manufacturing businesses as leaders in their industry, ready to meet the challenges of today and tomorrow.
Comentários