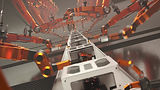
AvizOps AI Q™
Cognitive AI-Based Quality Analyst
Manufacturing operations often face several challenges related to quality management of the raw materials and finished products. Essentially a manufacturing operation needs to ensure the right Quality Control, Quality Assurance, and Quality Improvements
Inconsistent Quality Inspections
High Inspection Costs and Labor Intensity
Delayed Defect Detection
Inefficient Use of Data
Maintenance Challenges
Difficulty in Detecting Subtle Defects
Elevate Quality with cognitive AI bases Quality Analyst (CAQA)
With the capabilities CAQA leveraging advanced computer vision, sound analysis, and time-series data analysis, the following inspections can be carried out:
Visual Inspection:
-
Defect Detection: Identify surface defects such as scratches, dents, discoloration, or deformities.
-
Dimensional Accuracy: Measure dimensions and ensure they meet specified tolerances.
-
Pattern Recognition: Detect anomalies in patterns or shapes that indicate defects.
Sound Analysis:
-
Acoustic Emission Testing: Analyze sound waves produced by materials under stress to detect cracks or weaknesses.
-
Noise Quality Assessment: Ensure products meet noise emission standards and detect unusual sounds indicating defects.
-
Vibration Analysis: Identify abnormal vibrations that could indicate mechanical issues.
Time-Series Data Analysis:
-
Operational Monitoring: Track performance data over time to identify trends and predict failures.
-
Process Stability: Ensure that manufacturing processes remain stable and within control limits.
-
Predictive Maintenance: leverages historical data to forecast maintenance needs before failures occur.
Integrated with CAQA, it sharpens defect detection, reduces inspection times and costs, and ensures top quality standards.

How AI Q brings about this?
Visual Inspection-
Defect Detection:
-
AI Algorithms: The solution leverages machine learning algorithms to automatically detect surface defects such as scratches, dents, discoloration, or deformities in real-time.
-
High-Resolution Cameras: We deploy high-resolution cameras to capture detailed images of products for thorough inspection.
-
Image Processing: Apply advanced image processing techniques to highlight and classify defects.

Visual Inspection
Dimensional Accuracy:
-
3D Scanning: We leverage 3D scanning technology to measure product dimensions accurately and ensure they meet specified tolerances.
-
Calibration Systems: We integrate automated calibration systems to maintain precision in measurements.
Pattern Recognition:
-
Machine Learning Models: We train machine learning models to recognize and detect anomalies in patterns or shapes, indicating potential defects.
-
Automated Inspection: Implement automated inspection systems that continuously monitor and compare product patterns against standard templates.

Sound Analysis
Sound Analysis-
Acoustic Emission Testing:
-
Microphone Arrays: We deploy arrays of sensitive microphones to capture sound waves produced by materials under stress.
-
Signal Processing: We use advanced signal processing techniques to analyze acoustic emissions and detect cracks or weaknesses.
Noise Quality Assessment:
-
Standard Compliance: We ensure products meet noise emission standards by continuously monitoring sound levels during production.
-
Anomaly Detection: Detect unusual sounds that may indicate underlying defects or malfunctions.
Vibration Analysis:
-
Vibration Sensors: We install vibration sensors on machinery and equipment to continuously monitor for abnormal vibrations.
-
Predictive Models: We have developed predictive models to identify patterns in vibration data that could indicate mechanical issues.
Time-Series Data Analysis-
Operational Monitoring:
-
IoT Integration: We have integrated Internet of Things (IoT) devices to collect performance data from machinery and production lines in real-time.
-
Data Visualization: We use data visualization tools to track and display performance metrics over time, identifying trends and anomalies.
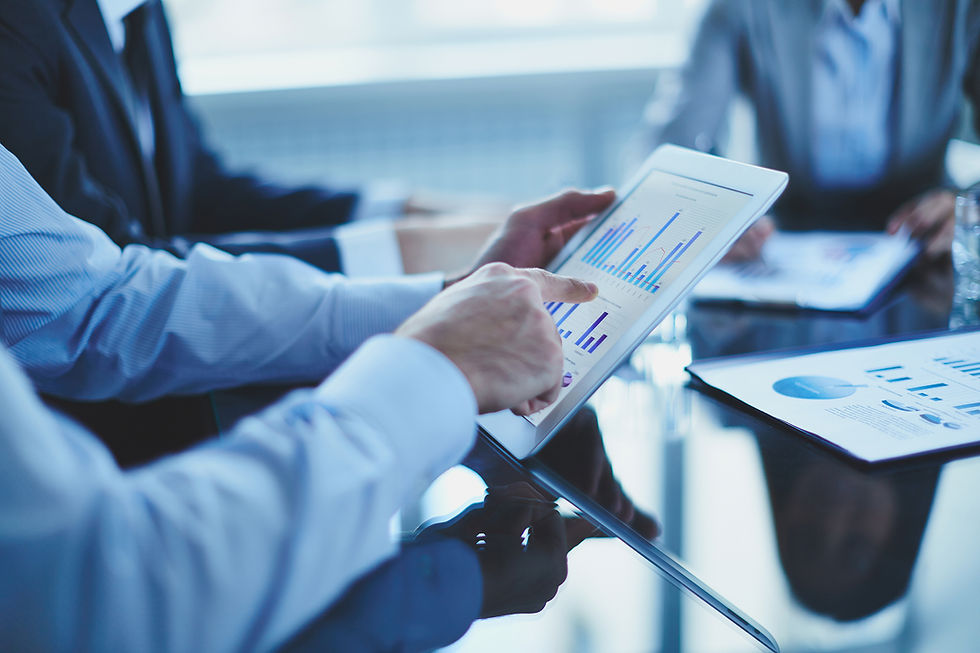
Time-Series Data Analysis
Process Stability:
-
Control Charts: We have implemented control charts to monitor manufacturing processes and ensure they remain stable and within control limits.
-
Statistical Analysis: Apply statistical analysis techniques to identify variations and take corrective actions promptly.
Predictive Maintenance:
-
Historical Data Analysis: We analyze historical data to predict when maintenance is needed before a failure occurs, reducing downtime and maintenance costs.
-
Machine Learning: We use machine learning algorithms to build predictive maintenance models that can forecast equipment failures based on historical and real-time data
© 2024 Avizops Solutions (OPC) Pvt. Ltd. All rights reserved.